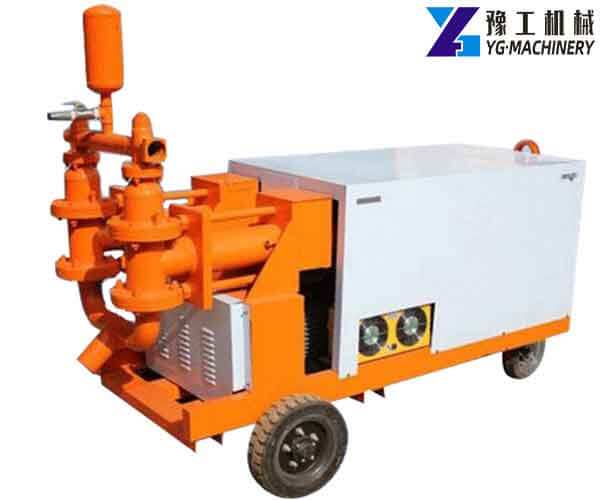
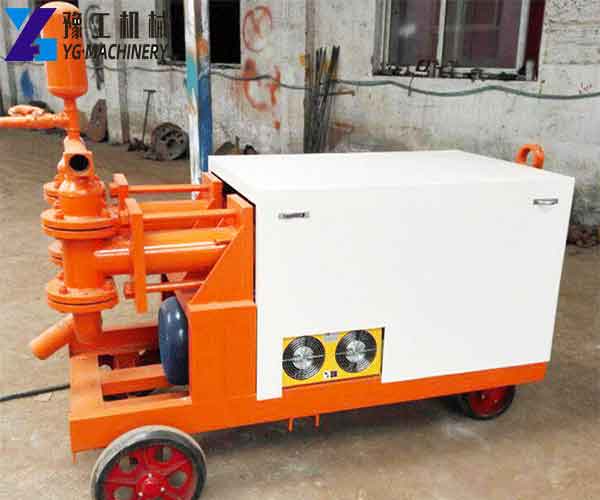
A hydraulic mortar pump uses high pressure to accurately inject solids or mixtures (water, cement slurry, mortar, etc.) into cracks and cavities in a rock formation or soil to reduce water seepage and consolidation of rock formations and soil. It is used as a medium for high-pressure infusion of water, cement slurry, mud, mortar, etc. It can also be used as a water purifier, sewage machine, and mud machine. It is widely used in tunnel excavation and maintenance, mine engineering, and the construction of dams, large bridges, and high-rise buildings. Mortar transport and grouting for engineering and various underground projects. 【WhatsApp/WeChat/Phone/Skype】+86 136 1385 6800
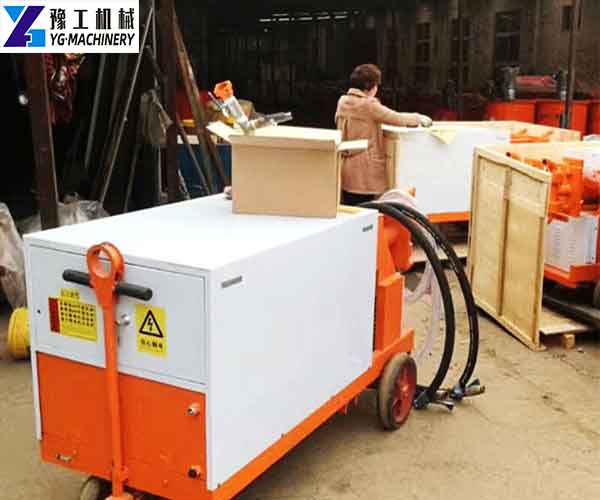
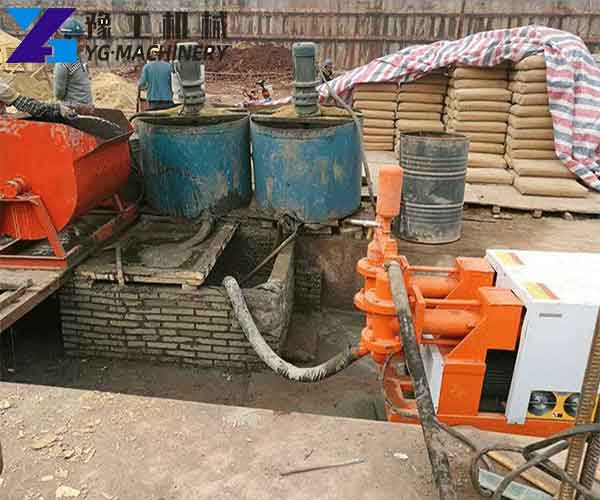
Hydraulic Mortar Pump Parameter:
Hydraulic Mortar Pump | |
Model | YG-200 |
Power | 15 KW |
Working Pressure | 0-16 Mpa (Adjustable) |
Working Capacity | 10 m3/h (Adjustable) |
Outlet Diameter | 38 mm |
Inlet Diameter | 64 mm |
Conveying Distance | Horizontal 200m Vertical 80m |
Max Particle Size | 10 mm |
Dimensions | 1800*1020*1600 mm |
Weight | 650 kg |
Cement Mortar Pump Features:
- In double cylinder double action, the piston reciprocates once, which can realize the suction and discharge of two liquids.
- Hydraulic drive, stable performance, reliable work, high pressure, easy to operate.
- The non-contact reversing mechanism can effectively reduce the failure rate and machine noise, and can also be applied to workplaces with special requirements ( explosion-proof ).
Hydraulic Mortar Pump Use Range:
- Sulfuric acid phosphate industry: Transportation of dilute acid, sewage, seawater, fluorosilicic acid-containing silica gel, phosphoric acid slurry, and other media.
- Non-ferrous metal smelting industry: It is especially suitable for various acid liquids such as lead, zinc, gold, silver, copper, manganese, cobalt, rare earth, etc., corrosive pulp, slurry ( for filter press) electrolyte, medium transportation such as sewage.
- Chemical and other enterprises: Various liquid or slurry positions of sulfuric acid, hydrochloric acid, alkaline, and oil. Production of titanium dioxide, iron-red powder, various dyes, pigment production, non-metallic mineral processing, and other industries.
- Chlorine alkali industry: Hydrochloric acid, liquid alkali, electrolyte, etc.
- Water treatment industry: Pure water, high-purity water, sewage ( leather sewage, electroplating sewage, electronic sewage, papermaking sewage, textile sewage, food sewage, domestic sewage, pharmaceutical industry sewage, etc.).
- Steel enterprises: Sulfuric acid and hydrochloric acid posts in pickling systems, and sewage with impurities.
- Wet desulfurization circulating pump: It can be used for alkaline, acidic, and corrosive jobs at the same time.
- Corrosive liquids in the coal industry and coal chemical industry, coal slurry transportation; Washing, and coal blending pumps.
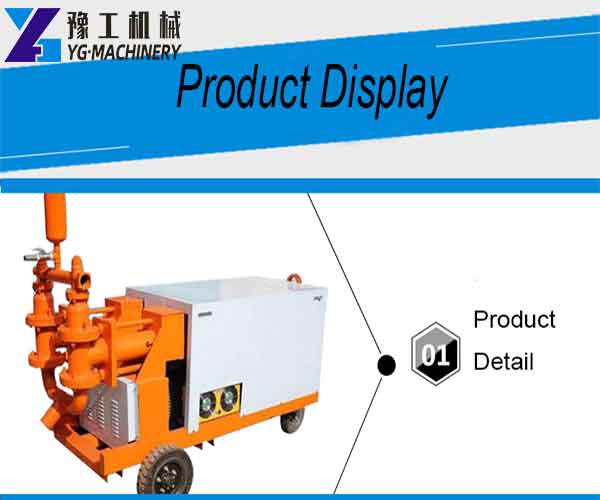
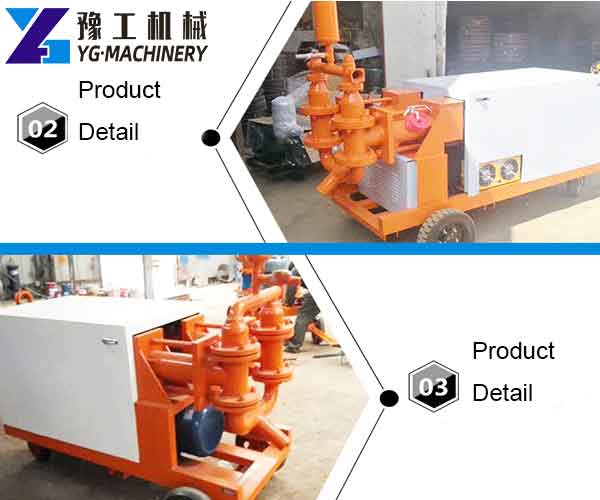
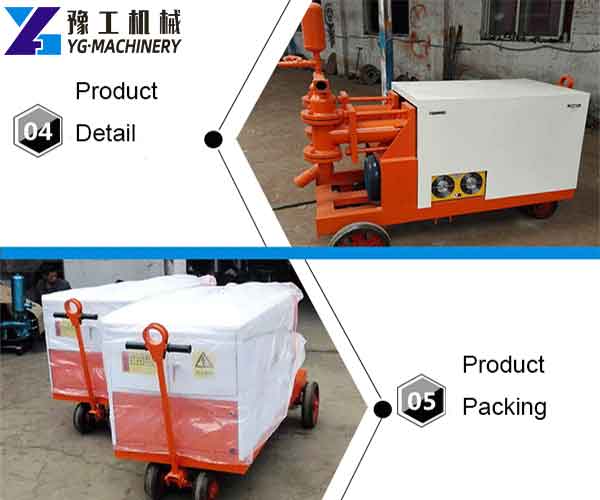
Operation and Maintenance Procedures:
-
Check Before Operation:
Before the test run, the coupling or shaft should be moved by hand to check whether the steering is correct and the operation is flexible. If the disc does not move or there is an abnormal sound, it should be checked in time. Check whether the coupling is horizontal from the outside by hand. Check whether the position of the lubricating oil is near the centerline of the oil mirror from the oil mirror hole on the bearing seat ( too much should be put off, too little should be added ), check the side, and move, if the problem still exists, it is necessary to disassemble the pump for inspection. ( Please refer to the structural diagram and disassembly procedure in the instruction manual when cleaning the pump ) to clean up the foreign objects, and contact the manufacturer to negotiate a solution.
-
Driving Steps:
- Filling the pump with liquid.
- Open the inlet valve in time ( if the inlet valve is a one-way check valve, no manual operation is required).
- Turn on the power.
- Open the outlet valve again.
-
Run:
If there is an abnormal sound during operation or abnormality such as motor heating, stop the inspection.
-
Shutdown:
- First, close the valve at the exit.
- Cut off the power supply and close the valve at the inlet in time; ( if the inlet valve is a one-way check valve, no manual operation is required).
-
Maintenance:
- The lubricating oil in the bearing housing should be replaced regularly, and the normal condition should be replaced once every six months.
- In the cold season, if there is ice formation after stopping the pump, first turn on the cooling water in the seal. If necessary, heat the water to thaw. Then move the coupling by hand until the operation is flexible. Then follow the startup procedure.
- The pump with a cooling water device should be connected to the cooling water before driving. When the pump is in normal operation, it can continue to be connected. If the conditions are not allowed, they can be stopped. The flow and pressure of the cooling water are not required. Tap water is can.
- The operation of the pump when closing the outlet valve is called the closed-pressure operation state. The closing operation time of the whole plastic pump or the plastic-lined pump should be shortened as much as possible. The medium temperature medium is limited to not more than 5 minutes, and the high-temperature medium is the most. Good not to exceed 2 minutes.
- The pump of the middle split pump casing, such as the pump with an inlet of 150mm or more, the sealing plastic at the middle split surface, due to some changes in the thermal expansion and contraction size, the installation bolt should be tightened first, then the inlet is connected. Pipeline to prevent leakage in the middle face, this article is especially important for users in the north.
- The pump cannot bear the weight of the inlet and outlet pipes. The shorter the inlet pipe, the better. The vertical height of the pump outlet to the valve should be as short as possible.
- Keep the water on the motor to prevent the motor from getting wet.